
NYMO - Adapting Offshore Engineering and Fabrication for the Future
By Tomas Jakobsen, BuildingPoint Scandinavia
The offshore engineering and fabrication industry faces challenges but also opportunities, both technologically and in the marketplace.
With shifting customer demands and an increasing need for digitalization, companies must adapt quickly to remain competitive.
In this article, based on a conversation with Mikkel Erichsen, Rune Johannesen, and Kjetil Kile, we explore how Nymo navigates these challenges, builds on its strengths, and prepares for the future!
SHORT VIDEO: Connecting the digital and physical worlds at Nymo’s fabrication site in Grimstad
An Industry in Transition
Companies in the engineering, procurement, and construction (EPC) sector for offshore projects face several complex challenges. Nymo, a company in the J.J. Ugland group, is now positioning itself to deliver beyond traditional oil and gas projects.
Nymo is exploring opportunities in offshore wind and aquaculture, and also sees potential in the electrification of existing fields, driven by the industry's desire to reduce emissions from offshore oil and gas production.
As a player with long-standing experience (the company was established in 1946) and a large number of deliveries to offshore operators, Nymo has many advantages. They have a strong digital infrastructure, with Tekla Structures being a part of their operations for many years, and modern machinery in their workshops capable of utilizing digital data.
The company has found that while digital modeling and 3D technology have improved many aspects of production, integrating various systems still poses challenges.
"One of our biggest challenges is ensuring efficient data flow throughout the value chain, especially when it comes to the integration between our ERP systems and material management," says Mikkel Erichsen, Corporate Engineering Manager at Nymo AS.
Another challenge is maintaining high-quality deliveries while managing increasingly complex projects. This requires not only technological expertise but also the ability to adapt to continuous changes and revisions in design and fabrication, which is particularly difficult when much of the engineering work happens in parallel processes, rather than sequentially over longer periods, as was more common a few years ago.
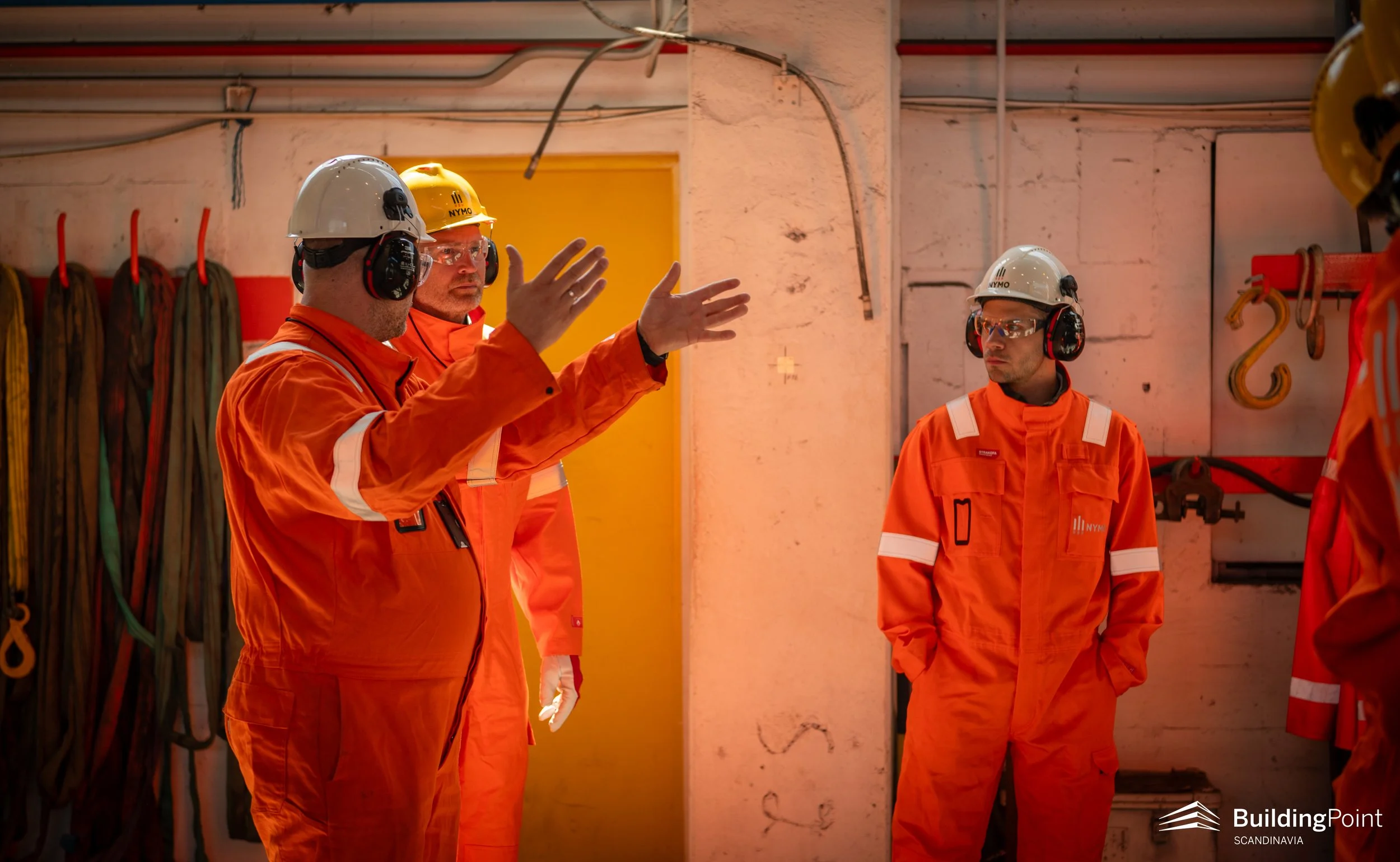
"
One of our biggest challenges is ensuring efficient data flow throughout the value chain…
- Mikkel Erichsen
Corporate Engineering Manager at Nymo AS.
Digital fabrication with Tekla Structures
To meet these challenges, Nymo has implemented digital solutions over several years, with Tekla Structures being a key tool in engineering for fabrication, achieving significant results with this approach.
Tekla Structures and E3D
In some of Nymo’s projects, they handle the overall design themselves. For example, in the KNARR FPSO (on the UK continental shelf) and Troll C (Norwegian continental shelf), two projects related to the electrification of oil and gas production, the steel design is done in Tekla, while other disciplines are handled in E3D, with continuous synchronization between the systems.
In other cases, Nymo starts their part of the work after the overall design has been done in E3D, focusing on engineering for fabrication.

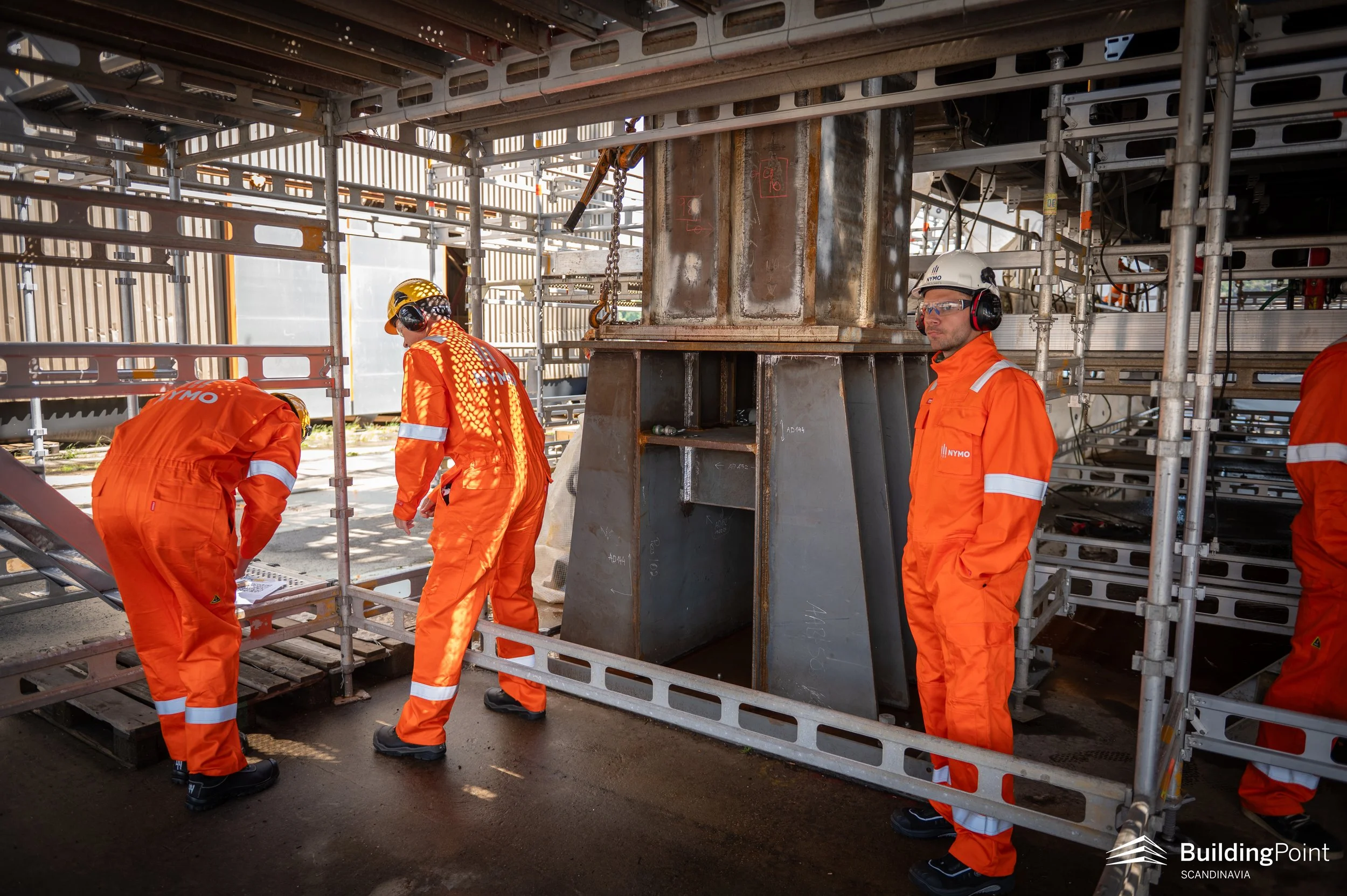
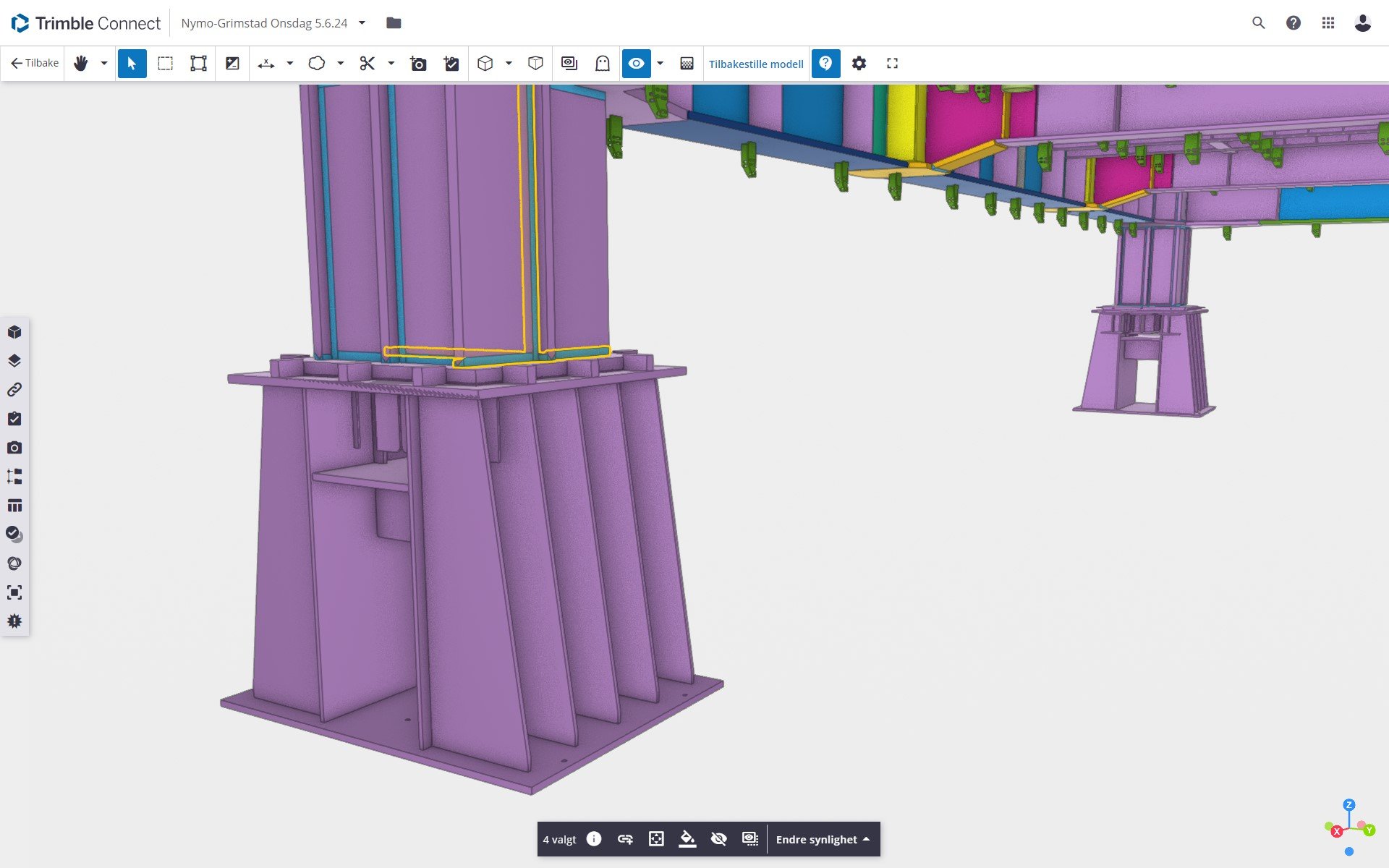

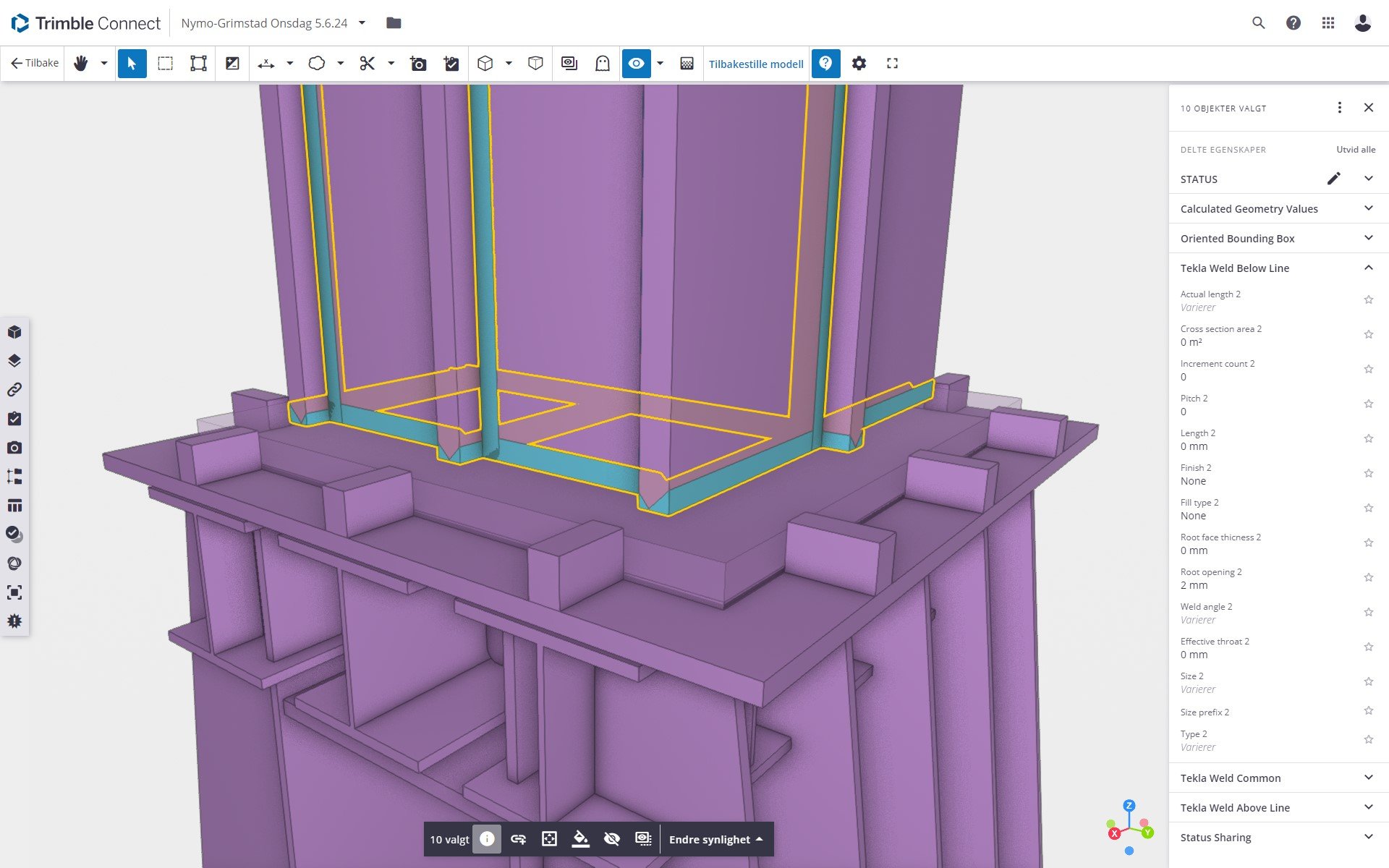
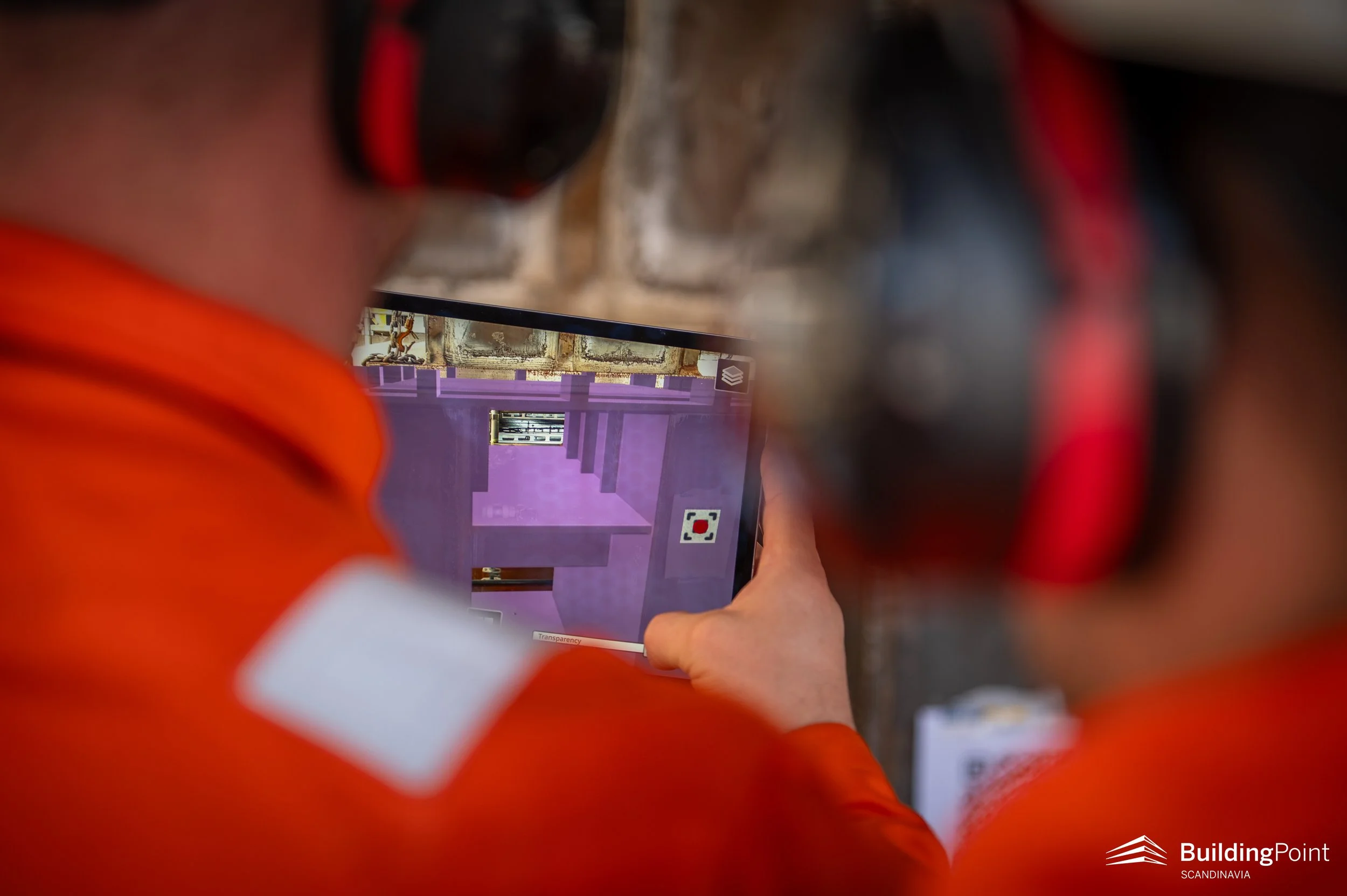

Detailing
Nymo then details the model in Tekla, adding the "important" welds, numbering them and including them in weight and COG (Center of Gravity) calculations.
They also add weld grooves in the Tekla model to produce accurate NC files for the ProCAM and HGG cutting machines.
Additionally, they incorporate other details, such as stairs, railings, and pipe supports.
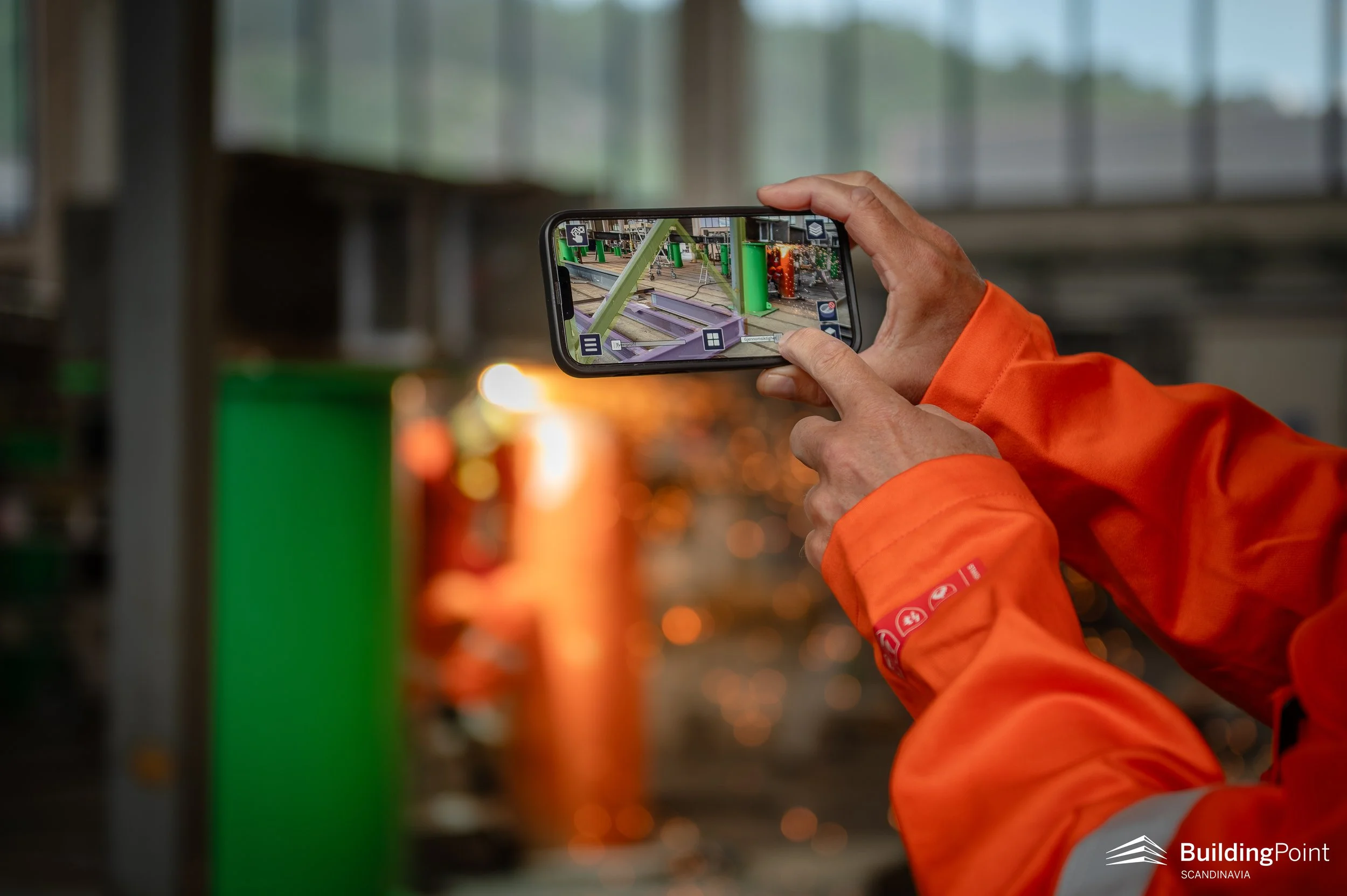
"
We are producing increasingly better digital models and we can, in many cases, fabricate directly from the model.
- Mikkel Erichsen
Corporate Engineering Manager at Nymo AS.
Standardization
By using Tekla Firm Settings, Nymo has enforced standardization across projects and teams, resulting in more consistent production data and reduced need for discussions, clarifications, and changes to the model. The Tekla files are taken into ProCAM and prepared for cutting. Fabrication time and costs are reduced, while quality is maintained.
Kjetil Kile, CAD Manager at Nymo, says: "We have successfully implemented Tekla in our engineering department, and it has become an invaluable tool for standardizing our processes. The software is becoming easier to use, and with Tekla Firm Settings, we can enforce unified standards across our projects."
"
We have successfully implemented Tekla in our engineering department, and it has become an invaluable tool for standardizing our processes.
The software is becoming easier to use, and with Tekla Firm Settings, we can enforce unified standards across our projects."
- Kjetil Kile
CAD Manager at Nymo
He further explains that this standardization enables all employees to work in a consistent and efficient manner, contributing to increased productivity and quality. This has been especially important at a time when Nymo has a high workload and needs to rely on temporary labor. He also highlights that collaboration with BuildingPoint Scandinavia's support team helps solve problems and increase efficiency.
Mikkel Erichsen is pleased with the progress but sees potential for even greater impact: "Although we have made significant advancements, we are still dependent on superusers to solve complex problems. Our goal going forward is to streamline processes so that we can reduce this dependency and work even more efficiently."
Nymo continually assesses the modeling process to find the optimal balance between what should or should not be modeled as a 3D object with all the necessary information. This can help reduce the need for drawings even further than today. This approach could provide many downstream benefits in terms of MTO (Material Take Off) reports for welding, weld symbols on assembly drawings, production planning, cost estimates, quality control, and Life Cycle Information (LCI).
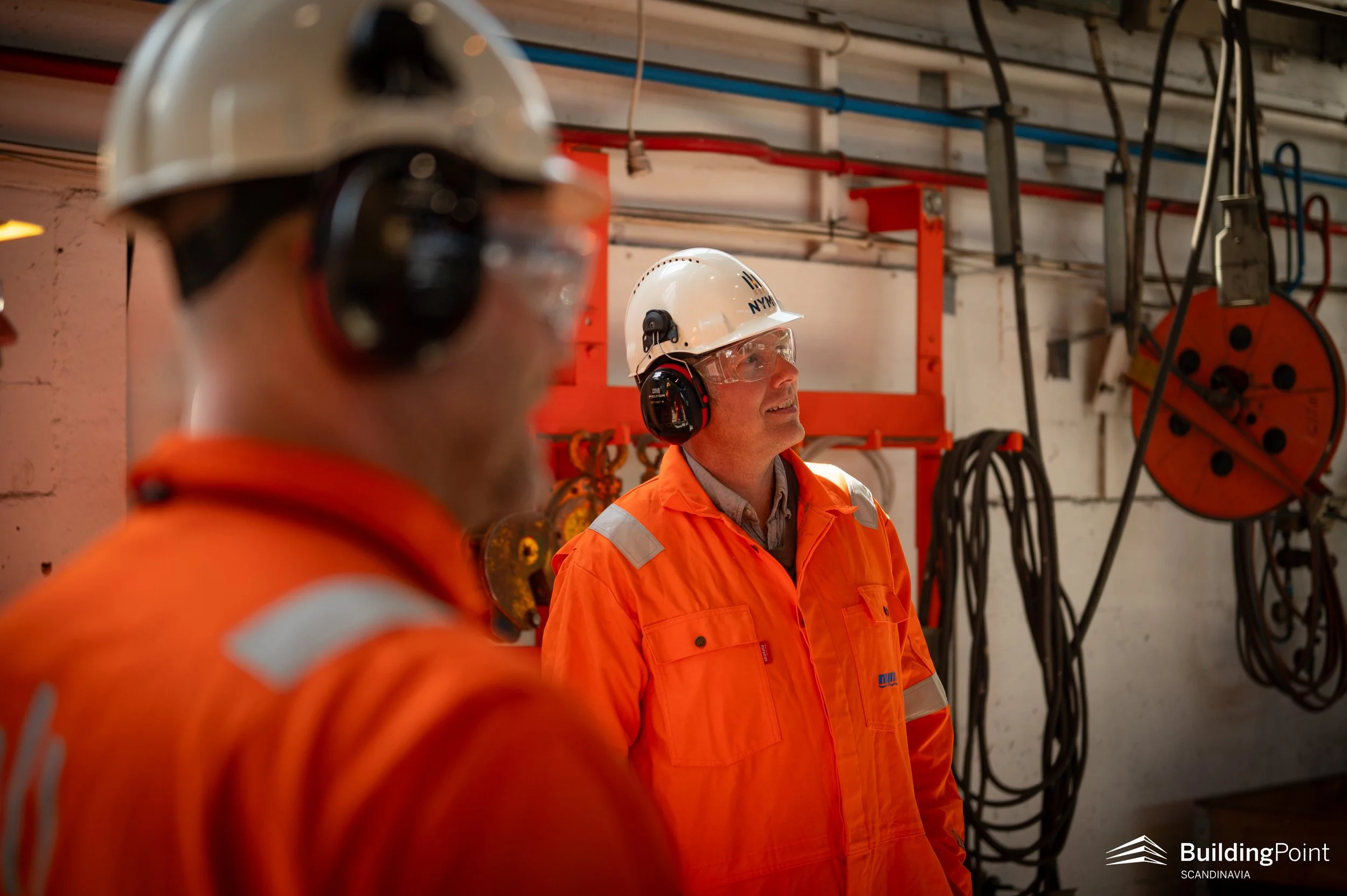
"
The Valhall PWP – Fenris project has been a key proof of our ability to manage complex, integrated processes, even when engineering and fabrication are done in parallel.
- Rune Johannesen
Lead Principal Engineer at Nymo.
Results
Nymo has already achieved significant results they are proud of. This includes successful projects such as the Valhall PWP – Fenris project:
"The Valhall PWP – Fenris project has been a key proof of our ability to manage complex, integrated processes, even when engineering and fabrication are done in parallel," says Rune Johannesen, Lead Principal Engineer at Nymo.
The company has demonstrated its ability to handle complex integrated processes with partners at multiple geographical locations. While there is still room for improvements that can increase the company's efficiency, their technological investments and systematic approach have already yielded positive results in projects. They have also helped position Nymo for future projects that will undoubtedly demand increased focus on time, quality, cost efficiency, and sustainability.

"
Unfortunately, contracts still require us to make many drawings as part of the delivery.
This costs us time and doesn’t move us into the future. There should be better solutions here, together with the operators, for the benefit of everyone."
- Mikkel Erichsen
Corporate Engineering Manager at Nymo AS.
The Future Requires Change
Looking ahead, the goal is to further improve and fine-tune digital workflows, especially through increased automation and better system integration, as well as the democratization of digital tools to enhance the value of the digital model across all phases of projects, from engineering to procurement, production, management, and maintenance.
Trimble Connect could be key to making models and other information available to everyone in the project on PC, tablet, and mobile phones.
Nymo is also exploring opportunities to reduce paper-based processes and move towards more model-based deliveries, although this will require changes both internally and with customers.
"We are producing increasingly better digital models and we can, in many cases, fabricate directly from the model. Unfortunately, contracts still require us to make many drawings as part of the delivery," says Mikkel Erichsen.
"This costs us time and doesn’t move us into the future. There should be better solutions here, together with the operators, for the benefit of everyone."
A central part of the strategy is also to improve the ability to run parallel processes in projects, where fabrication and engineering take place simultaneously. While this brings challenges, it is a deliberate strategy to reduce lead times and increase flexibility in project deliveries.
- END -
About Nymo
AS Nymo is a full-service engineering, procurement and construction company within the oil & gas and process industry.
Nymo offers total solutions to customers and has earned confidence for versatility, reliability, quality service, timely delivery, good project management and commitment to HSE excellence…
More about Nymo
More offshore related articles
Weld Preparation Tools in Tekla Structures
Tekla Structures has an extensive range of custom weld preparation components! Watch the demo video
AVEVA E3D + Tekla
Watch this demo of the process of transferring a model from AVEVA products (specifically PDMS, and applicable to E3D) to Tekla Structures!
Best practices for modeling tubes and beam connections in Tekla for fabrication with HGG machines
Get insights on machinery and fabrication workflows with Tekla, ProCam and HGG cutting machines!